Processless plate setting continues to advance
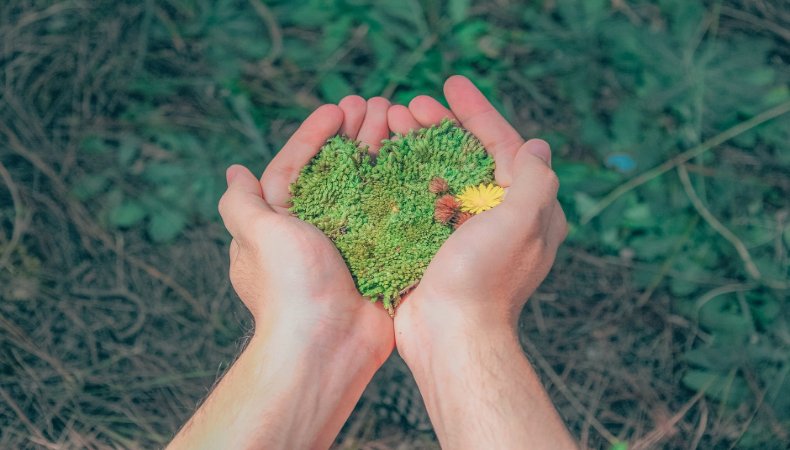
Laurel Brunner discusses the importance of processless plates in reducing processing steps from print production lines and increasing environmental sustainability. The main developers of processless plates are Agfa, Kodak and Fujifilm.
Processless plate setting is the next step in cutting processing steps from print production lines and making them more environmentally sustainable. Going processless does away with the plate processor, chemicals, disposal concerns and of course the man power and time involved in prepress.
The main developers of processless plates are Agfa, Kodak and Fujifilm which has recently announced a new addition to the options available on the market. New developments in this area are relatively few and far between, and Fujifilm has high hopes for the Superia ZE processless plate. For its latest iteration of the Pro-T plate launched in 2006 Fujfilm has developed a new coating technology. Interface Adherence and De-bonding (IAD) technology is an undercoat on the anodised plate that optimises plate development, even with low ink conditions.Fujifilm hopes it will help give Superia ZE the edge over Kodak’s Sonora and Agfa’s Azura and Eclipse lines.
For printers to make the switch, processless printing plate technologies have to provide the right price performance ratio. Performance concerns have been one of the biggest barriers to adoption of this technology even in printing plants where shorter runs, say 50,000 impressions, are the norm. Run length constraints are an obvious barrier, but there have been other problems such as latent image visibility, contrast, safelight handling, scratch resistance, efficiency of plate development on press, makeready times and performance with different inks. And then there is cost which, until these plates hit a point where manufacturers can benefit from economies of scale, remains higher than for plates which require processing. The savings in time, materials and energy should however make up for price differentials. People are after all quite an expensive resource.
Processless plate technology is reaching a level of maturity, however there is a constant trade-off between handling, getting the plate to develop quickly and consistently, and ensuring ink receptivity. We expect to see further refinements in the surface morphology and mechanical properties of a printing plate’s underlying aluminium, and of coating recipes. The combination of how plate surface, coatings and inks behave during development and on press will continue to improve and over time advances such as IAD will spread the appeal and viability of processless plates. They are already relevant for most commercial printers and will become relevant for all of them. This includes companies where very long run work dominates or where new UV presses are installed. From an environmental impact perspective, going processless should be a no brainer. It streamlines production, eliminates processing chemistries and water, and so saves money as well as cutting environmental impact.
Source Information: This article was produced by the Verdigris Project, an industry initiative intended to raise awareness of print’s positive environmental impact. This weekly commentary helps printing companies keep up to date with environmental standards, and how environmentally friendly business management can help improve their bottom lines. Verdigris is supported by the following companies: Agfa Graphics, EFI, Fespa, Fujifilm, HP, Kodak, Miraclon, Ricoh, Spindrift, Splash PR, Unity Publishing and Xeikon.